In industries like construction, logistics, and welding, safety gear like the construction safety vest—often synonymous with a reflective jacket—is non-negotiable. These garments ensure workers remain visible and protected in low-light or hazardous conditions. Partnering with reflective jacket manufacturers, particularly those offering OEM (Original Equipment Manufacturer) and ODM (Original Design Manufacturer) services, unlocks a range of underappreciated advantages. This article dives into six hidden benefits of such collaborations, optimized for readers seeking valuable insights into cost, customization, quality, and more. We’ll also debunk myths about slow delivery or regulatory ignorance while analyzing how reflective jacket manufacturers meet the diverse needs of brands, suppliers, and end-users in the branded reflective jacket market.
1. Cost Efficiency Through Direct Partnerships
Choosing the right construction safety vest often starts with affordability, and working directly with reflective jacket manufacturers delivers significant savings.
1.1. Leveraging Bulk Production
Reflective jacket manufacturers excel at mass production, driving down costs through economies of scale. For instance, a typical reflective jacket might use 100% polyester fabric with a 300D Oxford weave—durable and cost-effective when produced in bulk. Brands ordering thousands of units benefit from per-unit prices that intermediaries can’t match, making it easier to offer competitive pricing in the workwear market.
1.2. Cutting Out the Middleman
By partnering directly with OEM reflective jacket producers, brands eliminate distributor markups and logistics fees. This streamlined approach reduces overhead, allowing savings to trickle down to customers—whether they’re construction firms or individual workers needing a reliable construction safety vest.
2. Customization for Unique Needs
A standout branded reflective jacket reflects a company’s identity and meets specific job demands. Reflective jacket manufacturers offering OEM and ODM services provide unmatched flexibility.
2.1. Free Material Options
The right fabric can make or break a reflective jacket. Manufacturers offer choices like waterproof 300D polyester with PU coating (offering 5000mm waterproofing) or breathable mesh with a 120gsm weight for hot climates. For example, construction workers might need a waterproof, tear-resistant construction safety vest, while porters prioritize lightweight, ventilated options. This freedom ensures every OEM reflective jacket aligns with its intended use.
2.2. Printing and Branding Flexibility
From simple logo embroidery to full-color digital printing on reflective strips (meeting ANSI/ISEA 107-2020 standards), reflective jacket manufacturers cater to all branding needs. This customization lets brands create a branded reflective jacket that’s both functional and visually distinct, enhancing recognition on job sites.
3. Superior Quality Control and Compliance
Safety is paramount when choosing a construction safety vest, and reflective jacket manufacturers ensure products meet rigorous standards.
3.1. Stringent Production Oversight
Reputable manufacturers like BOWINS Garment—with ISO 9001:2015 certification—conduct multi-stage quality checks, from testing reflective tape brightness (e.g., 330 cd/lx·m² for Class 2 compliance) to inspecting stitching durability. This ensures every reflective jacket withstands harsh conditions, giving brands and workers peace of mind.
3.2. Regulatory Expertise
A common misconception is that OEM reflective jacket producers lack understanding of safety rules. In reality, experienced reflective jacket manufacturers are well-versed in standards like OSHA, EN ISO 20471, and ASTM, ensuring compliance without guesswork. This expertise minimizes liability risks for brands distributing construction safety vests.
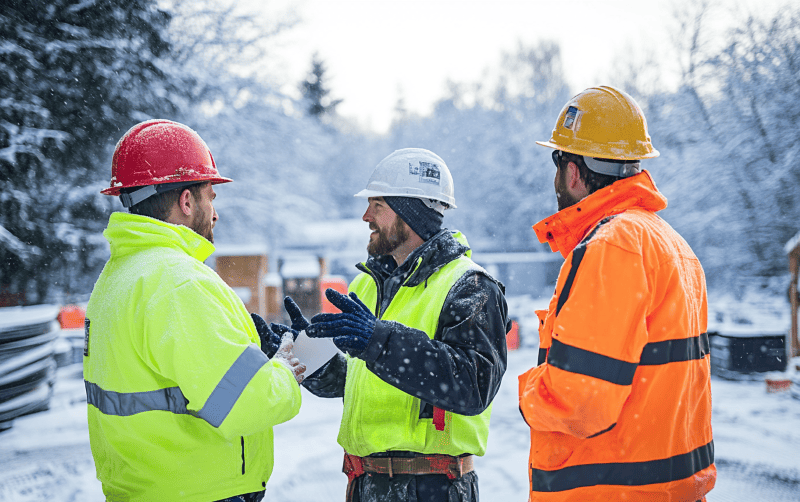
4. Faster Delivery Than You Think
Another myth about partnering with reflective jacket manufacturers is slow turnaround times. Direct collaboration proves otherwise.
4.1. Streamlined Production
With in-house facilities handling everything from cutting 300D Oxford fabric to sewing reflective tape, reflective jacket manufacturers shorten lead times. A typical OEM reflective jacket order might take 30-45 days—faster than multi-tiered supply chains—meeting tight deadlines for construction projects.
4.2. Global Logistics Advantage
Manufacturers with facilities in hubs like China, Cambodia, leverage efficient shipping networks. For instance, a company like BOWINS Garment uses its multi-country presence to expedite delivery, ensuring branded reflective jackets reach clients swiftly without compromising quality.
5. Innovation for Market Edge
Choosing the right construction safety vest means staying ahead of trends, and reflective jacket manufacturers drive innovation.
5.1. Collaborative Design
OEM and ODM partnerships often involve co-developing features like enhanced reflective strips (up to 500 cd/lx·m²) or ergonomic fits for all-day comfort. This collaboration results in a reflective jacket that’s both cutting-edge and practical, setting brands apart in competitive markets.
5.2. Prototyping and Feedback
Manufacturers assist with rapid prototyping—say, testing a breathable 150gsm polyester mesh—allowing brands to refine designs before launch. This reduces risks and ensures the final branded reflective jacket resonates with end-users, from welders to road crews.
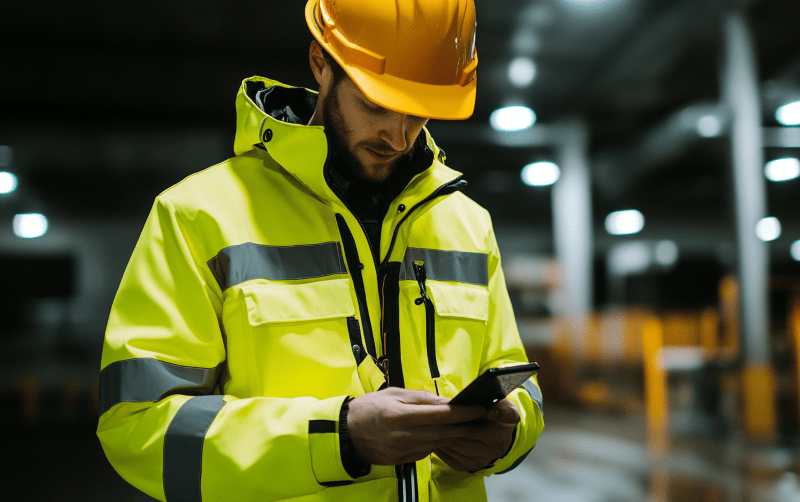
6. Meeting Diverse Customer Needs
Different stakeholders in the reflective jacket ecosystem—brands, suppliers, and workers—have unique demands, and reflective jacket manufacturers deliver tailored solutions.
6.1. ODM for Brands Without Designers
For companies lacking design teams, ODM services provide pre-engineered construction safety vests—think a standard Class 2 vest with 2-inch reflective tape and 120gsm fabric. This allows quick market entry with a compliant, ready-to-sell reflective jacket.
6.2. OEM for Design-Driven Brands
Brands with in-house creatives benefit from OEM flexibility, crafting custom OEM reflective jackets with specific specs—like 300D polyester with 8000mm breathability for rainy climates. This control ensures the branded reflective jacket matches exact job needs.
6.3. Suppliers’ Material Precision
Suppliers gain from consistent orders and precise material specs (e.g., PU-coated fabrics for waterproofing). Reflective jacket manufacturers align production with these needs, enhancing the quality of every construction safety vest delivered.
Conclusion: Choosing the Right Partner
Partnering with reflective jacket manufacturers transforms the way brands approach construction safety vests. From cost savings and customization to quality assurance and speedy delivery, these collaborations address myths and meet diverse needs head-on. For brands seeking a trusted ally, companies like BOWINS Garment shine. Since 2007, BOWINS has provided top-tier OEM/ODM services from its ISO 9001:2015-certified factories in China, with additional facilities in Cambodia.